آزمایشهای مخرب جوش
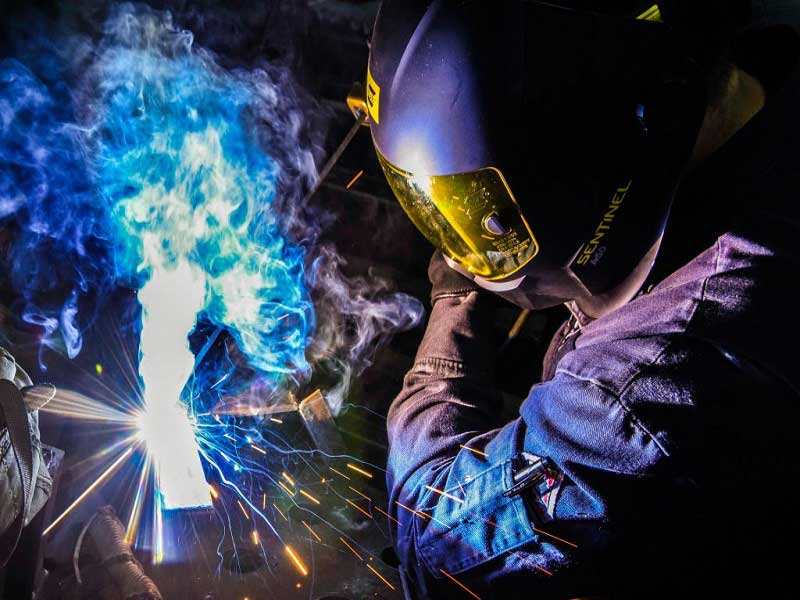
معرفی آزمایش مخرب
آزمایش مخرب عبارت است از آزمایش مکانیکی نمونۀ جوششده جهت تعیین مقاومت و سایر خواص مکانیکی. روشهای آزمایش از این نوع نسبتاً ارزانقیمت و بسیار کاربردی هستند، به همین جهت در سطح وسیعی جهت ارزیابی و تأیید دستورالعمل جوشکاری و صلاحیت جوشکار بهکار میروند. آزمایش مخرب معمولاً بر روی نمونۀ اخذ شده از ورق یا لولۀ جوششده انجام میشود که درحقیقت نمونهای از مصالح و دستورالعمل جوشکاری بهکاررفته در کارگاه یا کارخانه میباشند.
ضوابط عمومی
بهطورکلی در همۀ آییننامهها، ضوابط مربوط به ارزیابی دستورالعملهای جوشکاری ورقها و لولهها یکسان است و هر وضعیت جوشکاری، هر نوع درز اتصال و هر نوع جوشکاری یک شمارۀ مشخصۀ طراحی دارد. عموماً، نمونههای آزمایشی خمش رویه، خمش ریشه، و خمش جانبی برای جوشهای شیاری در ورقها و لولهها لازم است و آزمایش شکست گونیا و آزمایش حک برای جوش گوشه در ورقها موردنیاز میباشد. تعداد و نوع آزمایشهای لازم بسته به میزان ضخامت مصالح (ورق یا لوله) متفاوت است.
در اکثر آییننامهها، نتایج ارزیابیها بهصورت نامحدود معتبر هستند، مگر اینکه:
۱) جوشکار بر روی نوع جوشی که برای آن موردارزیابی قرار گرفته، بیش از ۶ ماه فعالیتی نداشته باشد. ارزیابی مجدد فقط برای ورق با ضخامت ۱۰ میلیمتر لازم است.
۲) دلیلی مبنی بر عدم صلاحیت جوشکار وجود داشته باشد.
درصورتیکه جوشکار در آزمون تعیین صلاحیت مردود شود، به روش زیر تحت آزمون مجدد قرار میگیرد:
۱) امتحان مجدد فوری، شامل دو آزمایش از هریک از مواردی که در آنها جوشکار مردود شده است. کلیۀ نمونههای آزمایشی در این گروه باید موردپذیرش قرار گیرد.
۲) یک امتحان مجدد کامل بعد از اینکه جوشکار تحت آموزش و تمرین مجدد قرار گرفت.
آییننامۀ AWS سه رده پذیرش با اسامی اختصاری AR-1 و AR-2 و AR-3 برای جوشکاری لولهها به رسمیت می شناسد:
۱) AR-1: برای بالاترین کیفیت جوشکاری نظیر جوشکاری تجهیزات لولهای نیروگاه اتمی و تجهیزات اکتشافات فضایی و همچنین در ساخت سیستم شیمیایی و گازی تحت فشار و دمای زیاد
۲) AR-2: برای جوشکاریهای با کیفیت زیاد نظیر سیستمهای خط لوله و لولههای تحت فشار
۳) AR-3: برای جوشهای با کیفیت اسمی نظیر تأسیسات منازل (تأسیسات آبی و حرارتی).
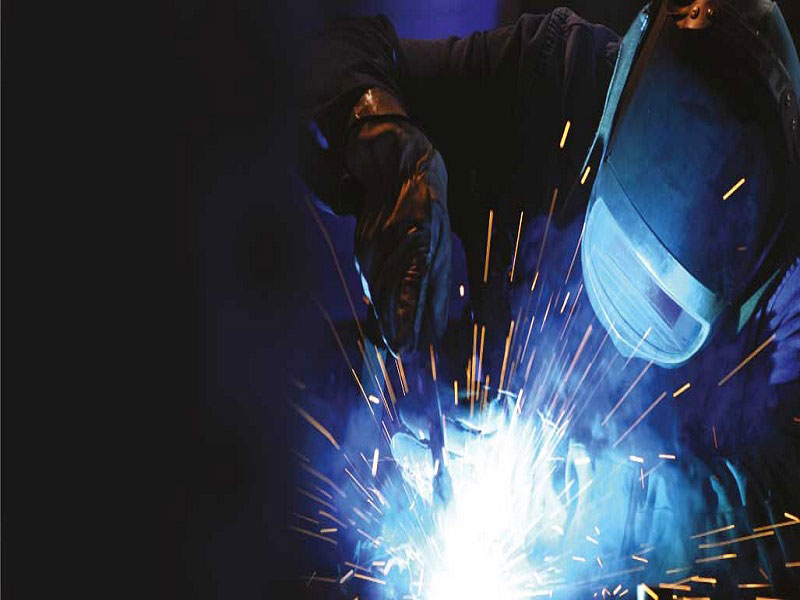
آزمایشهای ارزیابی دستورالعمل جوشکاری
این آزمایشها جهت تعیین صحت روش جوشکاری مورداستفاده در یک پروژۀ خاص انجام میگیرد. آزمایش ارزیابی دستورالعمل جوشکاری باید کلیۀ موارد نظیر مشخصات فلز پایه و فلز پرکننده، نحوۀ آمادهسازی درز اتصال، وضعیت جوشکاری، روش و تکنولوژی جوشکاری، و سایر مشخصههای جوشکاری را پوشش دهد. آزمایش باید شامل تنظیم شدت جریان، اندازه و کاربری الکترود، درجه حرارت پیشگرمایش، درجه حرارت پاسهای میانی و درجه حرارت پسگرمایش باشد.
آزمایشهای ارزیابی جوشکاران و اپراتورهای جوشکاری
این آزمایشها که آزمایش کیفیت اجرا نیز خوانده میشود، مشخص مینماید که آیا اپراتور دانش و مهارت انجام جوش سالم طبق دستورالعمل جوشکاری را داراست یا خیر. اغلب نمونهها مشابه نمونههای ارزیابی دستورالعمل جوشکاری است ولی تعدادشان کمتر است.
آمادهسازی نمونههای آزمایشی
نکتۀ قابلتوجه برای کارآموزان جوشکاری در ارتباط با جوشکاری نمونۀ آزمایشی این است که با وجود اینکه این آزمایشها برای تعیین توانایی جوشکاران طرح شده است، بسیاری از آنها به دلایلی که ارتباطی به قابلیتشان در جوشکاری ندارد، در امتحانات قبول نمیشوند. علت این امر بیدقتی در کاربرد جوش و بیتوجهی نسبت به آمادهسازی قطعۀ آزمایش و نمونههای آزمایشی است.
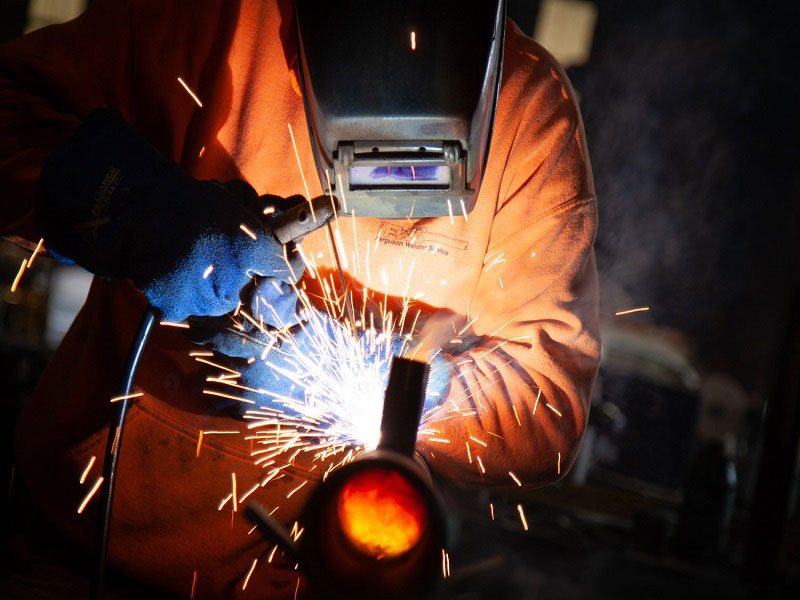
۱) انتخاب و آمادهسازی ورقها
در هنگام آزمایش ضروری است که ورق و تسمۀ پشتبندی جوشپذیر، شکلپذیر و از جنس فولاد کمکربن باشند. آزمایش بهگونهای طراحی شده است که هم ورق و هم خط جوش تحت خمش و کشش قرار میگیرند. اگر مقاومت کششی ورق خیلی بیشتر از مقاومت فلز جوش باشد، در حین آزمایش از محدودۀ تغییرشکلهای خطی فراتر نرفته و تمام تغییرشکلها به جوش اعمال میشود و درنتیجه تغییرشکل جوش فراتر از نقطۀ تسلیم شده و موجب گسیختگی در منطقۀ فلز جوش میگردد.
۲) جوشکاری ورقها
انتخاب صحیح الکترود اولین قدم در تولید یک جوش سالم میباشد. با توجه به اینکه ورقها عموماً در تمام وضعیتها جوشکاری میشوند، الکترود مورداستفاده برای ورقها باید مناسب برای تمام وضعیتها بوده و شکلپذیری مناسبی داشته باشد. مهمترین مرحله در اجرای جوش، پاس اول (یا پاس ریشه) در جوش شیاری و پاس ریشه در جوش گوشه میباشد. باید کوشش کافی از طرف جوشکار جهت نفوذ کافی، ذوب مناسب و سلامت فلز جوش در پاس ریشه انجام گیرد. هیچگونه عملیات اصلاحی توسط پیشگرمایش و پسگرمایش برای پذیرش آزمایش مجاز نیست. این امر باعث گرمشدن تدریجی ورق شده و باعث میگردد ورق بعد از تکمیل عملیات جوشکاری بهملایمت سرد شود. جوشکار تحت هیچ شرایطی مجاز نیست که قطعۀ جوششده را در آب سرد قرار داده و یا از هر طریق دیگری سردشدن قطعه را پس از جوشکاری تسریع کند.
۳) عملیات پرداخت نمونۀ آزمایشی
توجه کافی به پرداخت سطحی نمونۀ آزمایش ضروری است و عدم دقت در انجام آن میتواند باعث مردودشدن جوش سالم شود. پس از پایان جوش، عملیات تراشکاری و سنگزنی قطعه باید در امتداد طولی بر روی نمونه انجام شود. انجام این عمل در جهات دیگر موجب اثراتی خواهد شد که به شکست قطعه منجر میشود. هرقدر در عملیات پرداخت، سطح صافتری ایجاد گردد، شانس پذیرش نمونۀ آزمایشی بیشتر است. حتی یک شکاف عرضی باریک ممکن است تحت شرایط سخت تنشی آزمایش باز شود. درصورتیکه میزان نفوذ فلز مذاب در درز اتصال به میزان قابلتوجهی ناقص نباشد، (که در اینصورت جوش انجامشده غیرقابلقبول است) نوار جوش باید با سنگزنی یا ماشین ابزار صاف شود تا سطح خمشی تمیز و بدون ناهمواری بهوجود آید.
هرگونه گردۀ جوش (پاس تقویتی) چه در سطح رویی و چه در جوش ریشه باید زدوده شود. همواری لبههای نمونۀ آزمایشی باید شعاعی معادل ۱٫۵ میلیمتر داشته باشد که با برش تأمین میشود. پس از سنگزنی نمونه و هنگامیکه نمونه گرم است، هیچگاه آن را در داخل آب قرار ندهید. این عمل موجب ایجاد ترکهای ریز سطحی خواهد شد که تحت آزمایش خمش بزرگتر میشوند. پس از آنکه نمونۀ آزمایشی تحت خمش قرار گرفت، سطح محدب نمونه باید از لحاظ ترک، شکست و دیگر معایب کنترل شود. هر نمونهای که ترک و دیگر معایب (بازشدنی) آن ناشی از آزمایش خمش، بیش از ۳ میلیمتر در هر جهت دلخواه اندازهگیری شود، قابلقبول نیست. البته ترکهای ایجادشده در کنجهای نمونه در حین انجام آزمایش شامل این مطلب نیست.
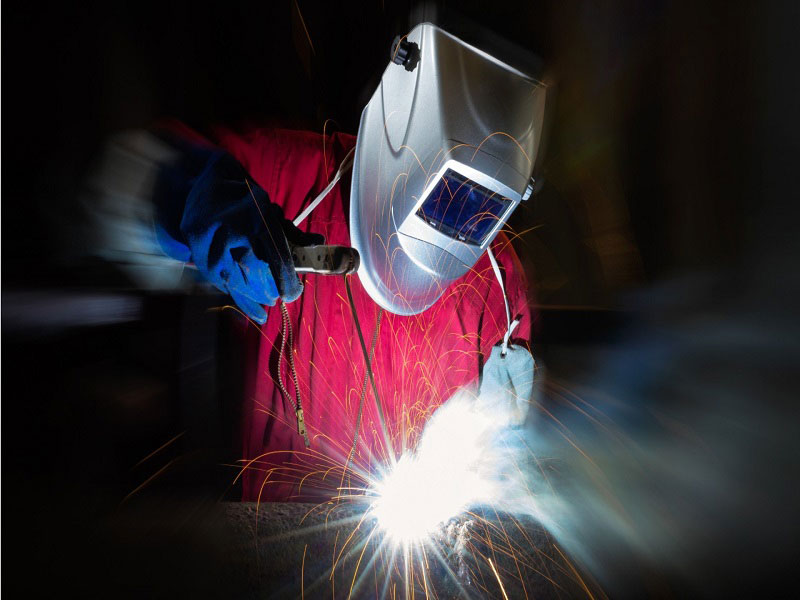
آزمایشهای سلامت جوش شیاری
۱) آزمایش کشش مقطع کاهشیافته
این آزمایش برای تعیین مقاومت کششی جوش و تنها بهمنظور ارزیابی دستورالعمل جوشکاری بهکار میرود. این آزمایش میتواند برای اتصالات لببهلب با جوش شیاری هم در ورق و هم در لولهها بهکار رود.
۲) آزمایش خمش آزاد
آزمایشهای خمش آزاد با هدف تعیین شکلپذیری فلز جوش بهکار میروند. این آزمایشها تنها برای ارزیابی دستورالعمل جوشکاری مورداستفاده قرار گرفته و بر روی جوشهای شیاری در اتصال لببهلب ورقها و لولهها انجام میشود.
۳) آزمایش خمش هدایتشده
آزمایشهای خمش ریشه، خمش رویه و خمش جانبی (خمش گونه) با هدف آشکارسازی عدم سلامت جوش، عدم نفوذ و امتزاج فلز جوش انجام میشود و برای ارزیابی دستورالعمل جوشکاری و صلاحیت جوشکاران مورداستفاده قرار میگیرد. این آزمایش در مورد جوشهای شیاری در ورقها و لوله اعمال میشود. آزمایش خمش رویه (خمش سطحی) کیفیت امتزاج فلز جوش در دیوارهها و سطح درز اتصال، تخلخل، تداخل گل و حفرههای گازی و دیگر معایب احتمالی را کنترل میکند. این آزمایش همچنین میزان شکلپذیری جوش را اندازه میگیرد. آزمایش خمش ریشه میزان نفوذ و امتزاج فلز جوش را در داخل ریشۀ درز اتصال کنترل میکند. آزمایش خمش جانبی بهمنظور کنترل سلامت و میزان ذوب فلز جوش میباشد.
۴) آزمایش شکست نمونۀ زخمدار
آزمایش شکست بر روی نمونۀ زخمدار با هدف تعیین سلامت جوش انجام میشود. این آزمایش در یک دورۀ زمانی کاربرد نسبتاً وسیعی داشت، ولی امروزه تعداد افراد کمی هستند که صلاحیت ارزیابی ساختمان بلورین مقطع شکسته شدۀ جوش را داشته باشند. بنابراین این آزمایش بهرغم دیگر آزمایشها چندان قابلاطمینان نیست.
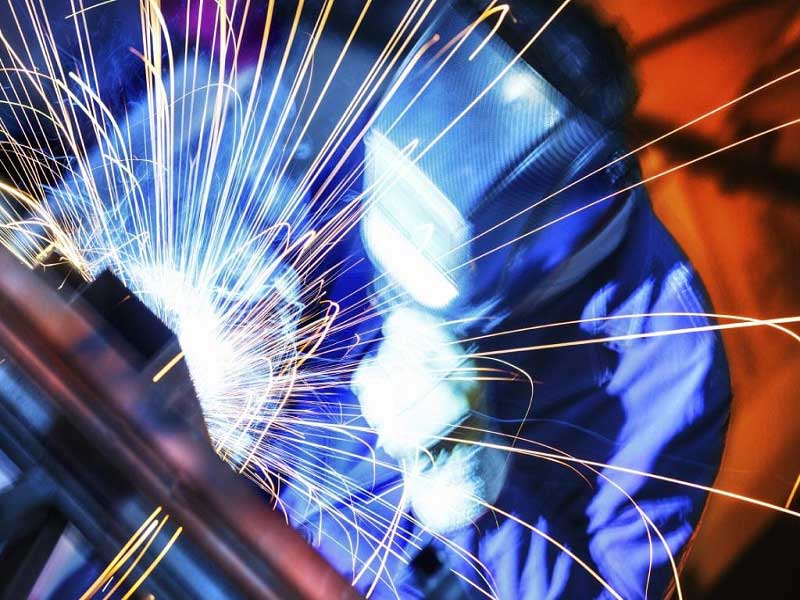
آزمایشهای سلامت جوش گوشه
۱) آزمایشهای برش طولی و عرضی
این آزمایشها مقاومت برشی جوش گوشه را تعیین میکنند و معمولاً برای ارزیابی نحوۀ اجرای جوشکاری بهکار میروند.
۲) آزمایش خمش هدایتشدۀ جوش گوشه
این آزمایش عدم سلامت فلز جوش در جوشکاری گوشه را مشخص میکند.
۳) آزمایش شکست جوش گوشه
این آزمایش با هدف تعیین سلامت جوش گوشه انجام میشود.
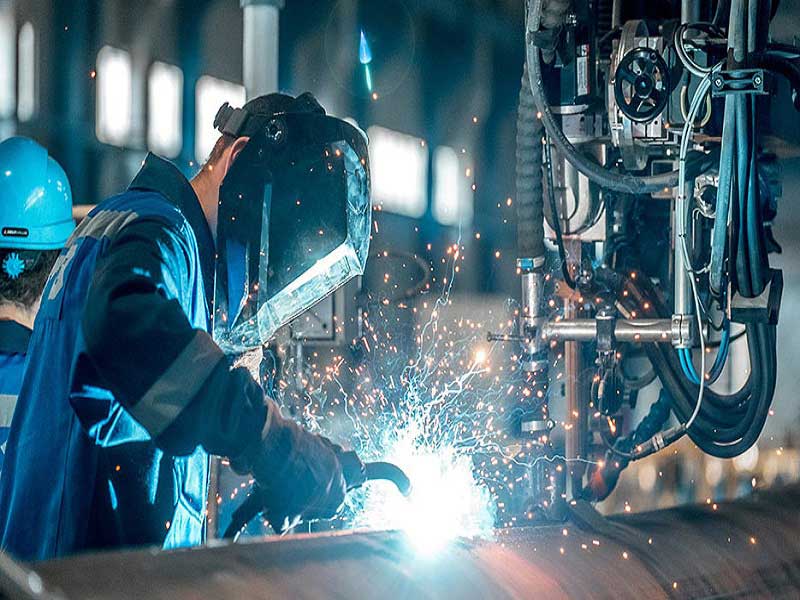
آزمایشهای دیگر
علاوه بر این آزمایشها، روشهای آزمایش دیگر نیز در صنعت جوشکاری نظیر آزمایش حک، ضربه، خستگی، خوردگی وجود دارند.
آزمایش حک
اغلب باید مقطعی از جوش تهیه شده و پس از حککاری برای عیبیابی موردبررسی قرار گیرد. روش حککاری میزان نفوذ فلز جوش و همچنین سلامت جوش را در مقطع موردنظر مشخص میکند. بررسی جوش در مقطع موردنظر با اهداف زیر دنبال میشود:
۱) تعیین سلامت جوش
۲) آشکارشدن مرزهای بین فلز جوش و فلز پایه و همچنین بین لایههای مختلف فلز جوش
۳) تعیین محل و عمق نفوذ جوش
۴) تعیین محل و تعداد پاسهای عبوری جوش
۵) بررسی متالورژی ناحیۀ تحت نفوذ حرارت (ناحیۀ تفتیده)
یک حککاری عمیق معایب بیضرری نظیر ترکها و تخلخلهای کوچک را بهطور اغراقآمیزی بزرگ نشان میدهد. بنابراین بازبینی سطحی باید به محض مشخصشدن واضح جوش انجام شود و حککاری نباید به میزانی باشد که موجب تخریب حجم داخلی نمونه گردد. سطح موردمطالعه ممکن است با استفاده از لایۀ نازکی از لاک الکل محافظت شود. در این صورت بازبینی سطح با استفاده از میکروسکوپ نور قطبی بررسی شده یا با دوربینهای مخصوص از ساختار داخلی آن عکس تهیه کرد. در این روش، یک مقطع عرضی از اتصال جوششده جهت عملیات حککاری بریده میشود. عمل برش درز اتصال با استفاده از یک ارۀ دندهریز انجام میشود. سطح فلز جوش و فلز پایه باید سوهان شود تا به یک سطح صاف تبدیل شده و سپس با سنبادۀ ریز پرداخت شود. این سطح با یکی از انواع محلولهای حککاری (ید و یدور پتاسیم، اسید نیتریک، اسید هیدروکلریک یا پرسولفات آمونیوم) آغشته میگردد.
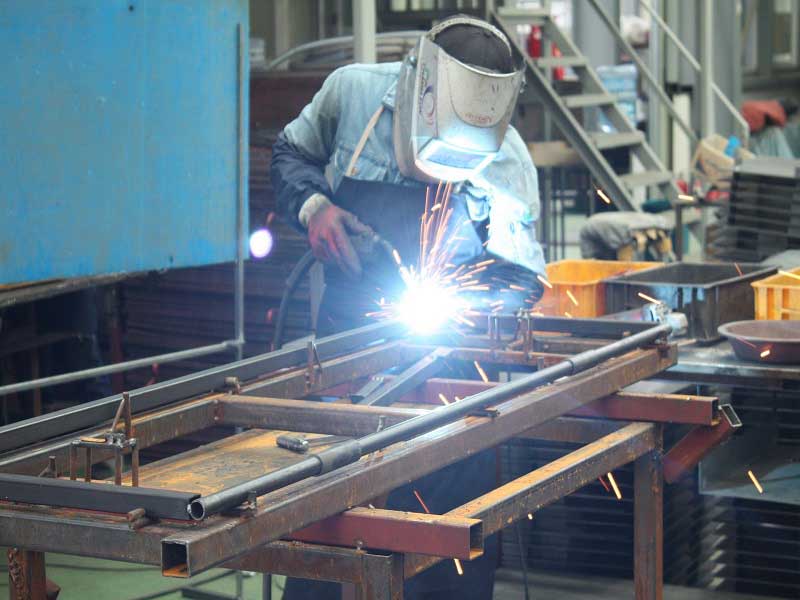
آزمایش ضربه
هدف از انجام آزمایش ضربه، تعیین مقاومت ضربهای جوش و فلز پایه در یک سازۀ جوششده میباشد. منظور از مقاومت ضربهای، طاقت فلز در مقابل ضربه ناگهانی و سریع میباشد. این آزمایش اطلاعات لازم در مورد مقایسۀ طاقت ضربهای فلز جوش و فلز پایه را فراهم میکند. یک جوش یا فلز ممکن است مقاومت کششی زیادی داشته و شکلپذیری بالایی در تنشهای کششی از خود نشان دهد ولی تحت اثر ضربات ناگهانی و سریع دچار شکستگی شوند که بهخاطر فقدان طاقت ضربهای مصالح است.
آزمونهای شارپی و ایزود
دو روش استاندارد برای آزمایش ضربهای وجود دارد: آزمایش ایزود و آزمایش شارپی. در این روشها نمونۀ آزمایشی با یک ضربه میشکند و مقاومت ضربهای نمونه برحسب واحد نیرو ـ طول که واحد کار و انرژی است، سنجیده میشود. (در فیزیک کار بهصورت حاصلضرب نیرو در جابهجایی نقطهاثر نیرو تعریف میشود).

آزمایش خستگی
آزمایش خستگی بهمنظور تعیین مقاومت جوش در مقابل تنشهای تکراری و مقایسۀ آن با مقاومت خستگی فلز پایه انجام میشود.
آزمایش شکست نمونۀ زخمدار
یک جوشکار یا بازرس میتواند طاقت فلز جوش یا فلز پایه را در کارگاه و بدون دسترسی به تجهیزات کامل و گرانقیمت آزمایش کند. این روش آزمایش نمونۀ زخمدار نامیده میشود. یک شیار با استفاده از اره یا وسیلۀ برنده در نمونۀ جوش یا ورق فولادی ایجاد شده و سپس نمونه در فک گیره قرار میگیرد. با استفاده از چکش ضربهای بهسمت شیاردار نمونه وارد میشود. میزان مقاومت ضربهای براساس نیروی لازم برای شکستن نمونه، مقدار لنگر ایجادشده در هنگام شکست و براساس کیفیت ظاهر سطح شکستهشده تعیین میشود.
منبع: راهنمای جوش و اتصالات جوشی در ساختمانهای فولادی، شاپور طاحونی، دفتر تدوین و ترویج مقررات ملی ساختمان، ۱۳۷۹